Embarking on a journey as a new embroidery business owner can be both exciting and challenging. As you set out to craft exquisite embroidered creations, you’ll soon realize that ensuring your embroidery equipment operates smoothly is paramount to your success.
However, even the most reliable machines encounter hiccups from time to time, and that’s where this guide comes in.
In this quick guide, we will delve into the art of troubleshooting embroidery equipment, all from the perspective of an operator. We understand that, especially in the early stages of your business, it’s crucial to tackle issues efficiently and with a keen eye.
So, whether you’re just starting out or looking to refine your skills, join us as we unravel the intricacies of troubleshooting your embroidery equipment for seamless stitching and beautiful creations.
In this article…
- The Importance of Reliable Equipment in Embroidery
- Common Equipment Problems in Embroidery
- Step-by-Step Troubleshooting Guide
- 3 Steps for Buying an Embroidery Machine with Equipment Financing
The Importance of Reliable Equipment in Embroidery
Starting an embroidery business is an exciting endeavor, filled with creativity and the promise of turning your passion into a profitable venture. However, as you embark on this journey, one critical factor that can’t be overstated is the significance of reliable embroidery equipment.
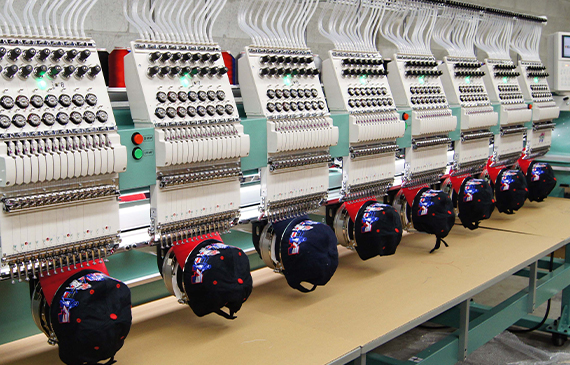
Your machines are the heart and soul of your operation, and they play a pivotal role in shaping the quality of your finished products and, ultimately, the success of your business.
Looking for reliable embroidery equipment, but worried about the cost?
Don’t stress! Financing can help you afford high-quality machines by spreading the payments over manageable monthly installments. Try Beacon Funding’s financing calculator now to see just how affordable your next machine purchase can be.
CALCULATE YOUR PAYMENT NOW
Why Does Equipment Matter?
Imagine your embroidery equipment as the artisans behind every beautifully stitched design. They are your trusted workforce, and their performance directly impacts the final result.
Here’s why dependable equipment is crucial:
- Consistency in Quality: Reliable equipment ensures that each embroidered item matches your design specifications with precision. This consistency is essential for building a reputation for high-quality products that customers can trust.
- Increased Productivity: Equipment that runs smoothly and without hiccups leads to higher productivity. You can fulfill orders efficiently, meeting deadlines and exceeding customer expectations.
- Reduced Downtime: Frequent equipment breakdowns or issues can lead to costly downtime, delaying orders and potentially frustrating customers. Reliable equipment minimizes these disruptions.
- Cost Efficiency: While investing in quality embroidery machines may seem insignificant initially, it often pays off in the long run. Durable equipment reduces repair and replacement costs, contributing to your bottom line.
- Customer Satisfaction: Ultimately, your customers’ satisfaction depends on the quality and timely delivery of their embroidered items. Reliable equipment helps you consistently meet and exceed their expectations.
- Reduced Labor Costs: Reliable equipment not only performs consistently but also does so quickly. This means your embroidery business can produce more items in less time. As a result, you may find that you don’t need as many employees on the shop floor, leading to cost savings in terms of salaries and benefits.
- Larger Operations: With reliable equipment in place, scaling up your embroidery production becomes a smoother process. You can easily add more machines to meet increasing demand without worrying about compatibility issues or constant maintenance.
Impacts on Your Reputation
A business with a track record of producing high-quality, well-crafted embroidery is more likely to attract repeat customers and referrals.
Picture a scenario where you receive an urgent order for custom-embroidered merchandise, and your equipment malfunctions. The consequences could be detrimental. Not only does it affect that specific order, but it can also harm your reputation, potentially leading to lost future business.
Common Equipment Problems in Embroidery
As a new embroidery business owner, it’s essential to be prepared for the common equipment problems you may encounter in your day-to-day operations. Recognizing these issues early and knowing how to address them can save you time, money, and headaches.
Let’s explore some of the most common equipment problems in the industry:
Needle Breakage
- Causes: Needle breakage can occur due to several factors, including using the wrong needle size, poor needle quality, or excessive speed.
- Solutions: Ensure you’re using the correct needle type and size for your fabric and design. Regularly inspect and replace needles and reduce machine speed if necessary.
Thread Tension Issues
- Causes: Incorrect thread tension can lead to loose or tight stitches. Common culprits include incorrect bobbin tension or threading errors.
- Solutions: Recheck thread paths, adjust thread tension as needed, and ensure proper bobbin winding and insertion.
Hooping Problems
- Causes: Hooping issues often result from uneven fabric tension, misalignment, or improper hooping techniques.
- Solutions: Practice precise hooping techniques, use stabilizers when necessary, and ensure fabric is evenly tensioned within the hoop.
Thread Breaks
- Causes: Thread breaks can occur due to thread quality, incorrect threading, or friction-related issues.
- Solutions: Invest in high-quality threads, double-check threading paths, and monitor thread spool rotation for smooth unwinding.
Stitching Errors
- Causes: Stitching errors encompass a wide range of issues, such as skipped stitches, thread loops, or misalignment.
- Solutions: Review and adjust your digitized design, ensure proper machine settings, and clean your embroidery machine regularly to prevent buildup.
These are just a few examples of the equipment problems you may encounter in your embroidery business. It’s important to note that many of these issues can overlap or have multiple potential causes. As a new embroidery business owner, it’s essential to approach troubleshooting systematically and methodically, starting with the basics.
Step-by-Step Troubleshooting Guide
Embroidery equipment problems can be frustrating, but they are often solvable with a systematic approach. As a new embroidery business owner, mastering troubleshooting techniques is an essential skill. Here is a step-by-step guide to troubleshoot common equipment problems effectively.
Step 1: Identifying the Problem – Recognizing Signs of Trouble
The first step in troubleshooting embroidery equipment is to identify the specific issue. Pay attention to the following signs of trouble:
- Irregular stitching patterns
- Thread breaks or thread tension problems
- Needle breakage or unusual noise
- Misalignment or shifting of designs
- Uneven or puckered fabric
By pinpointing the problem, you can proceed with a targeted solution.
Step 2: Checking the needle – Inspecting and Replacing Needles
- Turn off your embroidery machine and unplug it for safety.
- Carefully remove the needle, paying attention to its condition.
- Examine the needle for signs of damage or dullness, such as bent tips or burrs.
- Replace the needle with a new one that matches the fabric and design you’re working on.
- Ensure proper needle insertion, with the flat side facing the correct direction.
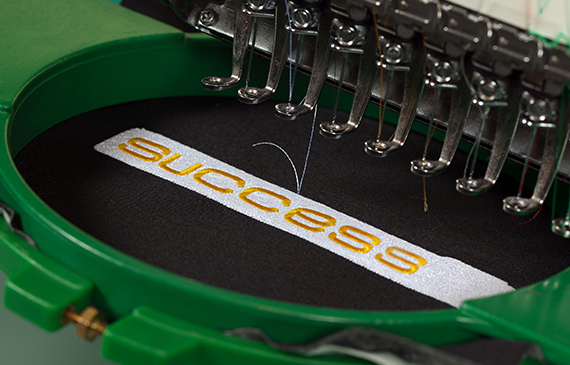
Step 3: Adjusting Thread Tension – Basics for Beginners
- Refer to your machine’s manual to locate the thread tension adjustment settings.
- Test your thread tension by sewing a sample on the same fabric you’re using for your project.
- If the stitches are too loose (looping on the bottom), increase the tension. If they’re too tight (puckering the fabric), decrease the tension.
- Make small adjustments and test again until you achieve balanced tension.
Step 4: Proper Hooping – Ensuring Fabric Stability
- Ensure the fabric is clean, flat, and free from wrinkles or folds.
- Select an appropriate hoop size for your design and fabric.
- Place the inner hoop underneath the fabric and the outer hoop on top.
- Tighten the hoop to secure the fabric, making sure it’s evenly tensioned.
Step 5: Bobbin and Bobbin Case Maintenance
- Remove the bobbin case according to your machine’s instructions.
- Check the bobbin for proper winding and tension. Rewind if necessary.
- Clean the bobbin area and bobbin case of any lint or debris.
- Reassemble the bobbin case correctly and ensure proper insertion.
Step 6: Adjusting Machine Settings – Simple Adjustments
- Refer to your machine’s manual to understand the settings relevant to your issue.
- Make minor adjustments to settings such as speed, stitch length, or presser foot pressure.
- Keep a record of your machine’s settings for different fabrics and designs.
Step 7: Testing and Monitoring – Quality Assurance
- Run a test stitch on a scrap piece of fabric before starting your project.
- Monitor the machine’s performance during stitching, watching for any signs of trouble.
- Continuously inspect the embroidery as it progresses to catch and address issues promptly.
Remember, troubleshooting embroidery equipment is a skill that improves with practice. It’s essential to document your troubleshooting process, noting the solutions that worked for specific issues. Over time, you’ll become more confident in diagnosing and resolving equipment problems efficiently, ensuring the smooth operation of your embroidery business.
3 Steps for Buying an Embroidery Machine with Equipment Financing
Step 1: Get pre-approved before you begin shopping
To ensure affordability, it’s crucial to establish your budget first. You can easily achieve this by obtaining pre-approval for embroidery financing, which comes at no cost and doesn’t require any commitment.
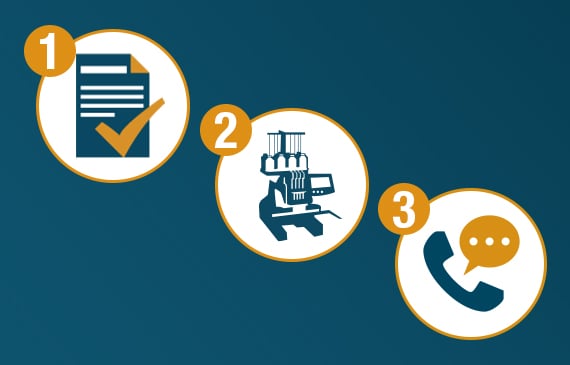
This step will also enable you to determine the monthly payment that comfortably fits your financial situation.
Step 2: Explore both new and used embroidery machines
One fantastic aspect of partnering with Beacon Funding is that age of the equipment doesn’t pose a hindrance to your acquisition. What’s even better is that if you come across equipment online, from a friend, or at a dealership, there’s a strong likelihood that Beacon Funding can provide the financing. This flexibility broadens your options, allowing you to acquire the equipment that suits your needs best.
Step 3: Contact Beacon Funding when you’ve identified your preferred equipment
Once you’ve determined the make and model of the equipment you require, reach out to Beacon Funding. Our team is ready to assist you in securing the embroidery machine you’ve always wanted. Schedule a call with your financing consultant today, and they will guide you through the process of preparing your digital application quickly.
SCHEDULE A CALL NOW